How 3D Printing Contributes to Next-Generation Spacecraft Design
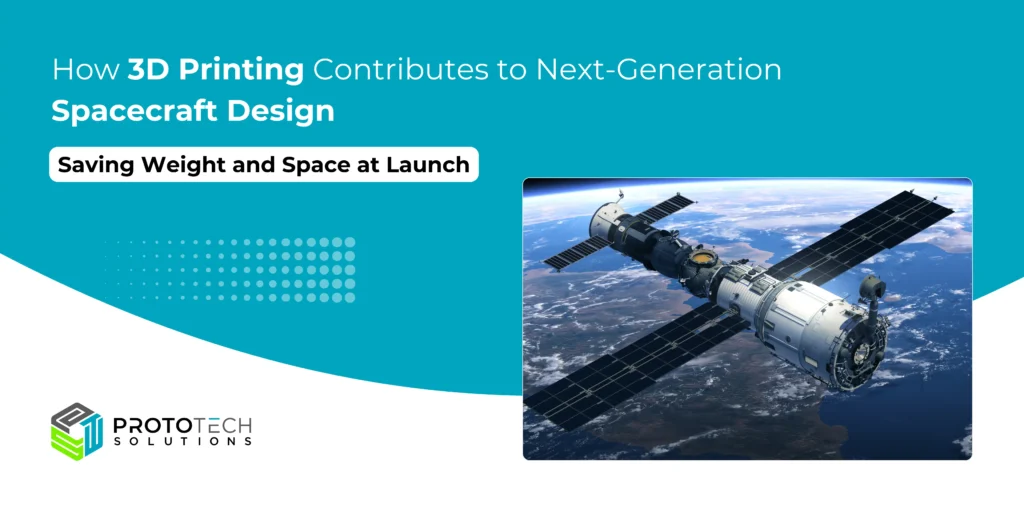
When you think about space exploration, your mind probably jumps to astronauts floating in zero gravity, distant planets, or the iconic images of rockets blasting off into the cosmos. But behind those awe-inspiring moments is a world of innovation happening right here on Earth, and one of the most exciting developments is the role of 3D printing in designing the next generation of spacecraft. This technology isn’t just a futuristic buzzword; it’s already revolutionising how we build the machines that will take us further into the universe than ever before. Let’s dive into how 3D printing shapes spacecraft components, from lightweight fuel tanks to complex engine parts, and why it’s such a game-changer for future space missions.
Why 3D Printing? The Need for Innovation in Spacecraft Design
3D printing, also known as additive manufacturing, is revolutionizing the aerospace industry and playing a crucial role in the design and production of next-generation spacecraft. This innovative technology is transforming the way we approach space exploration by enabling the creation of complex, lightweight, and cost-effective components.
The global 3D printing market is experiencing significant growth, driven by advancements in technology and increasing adoption across various industries. As of 2024, the market is valued at approximately USD 17.5 billion and is projected to reach USD 37.4 billion by 2029, reflecting a compound annual growth rate (CAGR) of 16.4%. Other analyses suggest even higher growth trajectories, with estimates of the market reaching USD 88.28 billion by 2030 at a CAGR of 23.5%.
Spacecraft have always been marvels of engineering, but they’re also incredibly challenging to design. Every ounce of weight matters, every component needs to withstand extreme conditions, and the cost of failure is astronomical—literally. Traditional manufacturing methods, like casting or machining, often involve multiple steps, heavy tooling, and a lot of wasted material. Enter 3D printing, or additive manufacturing, which builds objects layer by layer from digital designs. This approach allows engineers to create parts that are lighter, stronger, and more complex than ever before, all while reducing waste and speeding up production.
For space exploration, where efficiency and reliability are non-negotiable, 3D printing is like a breath of fresh air. It’s not just about making things faster or cheaper (though those are big perks); it’s about pushing the boundaries of what’s possible. Companies like SpaceX, NASA, and other space agencies are already harnessing this technology to build components that were once thought impossible, and the results are pretty mind-blowing.
Lightweight Fuel Tanks: Fueling the Future
One of the most critical parts of any spacecraft is its fuel tank. Fuel is heavy, and in space, every kilogram you launch costs a small fortune. That’s where 3D printing comes in, allowing engineers to design fuel tanks that are not only lighter but also more efficient. Traditional fuel tanks are often made from sheets of metal that are welded or riveted together, which can create weak points and add unnecessary weight. With 3D printing, you can create a single, seamless tank with intricate internal structures that optimize fuel storage and distribution.
For example, NASA has been experimenting with 3D-printed fuel tanks made from advanced materials like titanium or even composite polymers. These tanks can be designed with lattice structures inside, reducing weight without sacrificing strength. Imagine a fuel tank that looks like a piece of modern art—beautifully complex, yet perfectly functional. This isn’t science fiction; it’s happening now. Lighter fuel tanks mean spacecraft can carry more payload (like scientific instruments or supplies for astronauts) or travel further on the same amount of fuel. It’s a small change with a huge impact.
Complex Engine Parts: Precision at Its Best
Engines are the heart of any spacecraft, and they’re some of the most challenging components to design and build. Rocket engines, in particular, have to handle extreme temperatures, pressures, and vibrations while operating flawlessly in the vacuum of space. Traditional manufacturing often struggles to create the intricate geometries and internal channels needed for optimal performance. But 3D printing? It thrives on complexity.
Take, for instance, the combustion chambers in rocket engines. These need to be designed with cooling channels that snake around the chamber to prevent overheating during launch. With 3D printing, engineers can design and produce these chambers as a single piece, eliminating the need for multiple parts and potential failure points. SpaceX has already used 3D printing to create parts for its Merlin and Raptor engines, which power the Falcon 9 and Starship rockets.
What’s even cooler is that 3D printing allows for rapid prototyping. Engineers can test a new design, print it, and see how it performs—all in a fraction of the time it would take with traditional methods. This iterative process is crucial for pushing the boundaries of space technology, especially as we aim for missions to Mars and beyond.
Accelerating Development and Prototyping
The iterative nature of 3D printing significantly speeds up the research and development process for spacecraft components. Engineers can quickly design a part, print it, test it, identify flaws, make improvements, and repeat the process. This rapid prototyping capability allows for faster innovation and refinement of designs, ultimately leading to more advanced and efficient spacecraft.
Moreover, the ability to produce prototypes quickly and cost-effectively enables space agencies and private companies to test multiple design iterations before committing to final production. This approach not only saves time but also reduces overall development costs.
Enabling On-Demand Manufacturing in Space
Perhaps one of the most exciting prospects of 3D printing for space exploration is the potential for on-demand manufacturing in space. NASA has already successfully tested a 3D printer aboard the International Space Station, marking the beginning of a new era in space exploration.
The ability to produce spare parts and tools in space offers several advantages:
- Reduced reliance on Earth-based supply chains
- Decreased launch costs for replacement parts
- Increased mission flexibility and self-sufficiency
- Enhanced ability to respond to unforeseen challenges during long-duration missions
As 3D printing technology continues to advance, it may even become possible to manufacture entire satellites or spacecraft components in orbit, further revolutionizing space exploration and colonization efforts.
Enabling New Design Paradigms
3D printing is not just about replicating existing designs; it’s about enabling entirely new design paradigms. Engineers can now create structures and components that were previously impossible to manufacture, leading to innovative solutions for spacecraft design challenges.
For instance, the partnership between EOS and Hyperganic is taking design freedom to the next level for space propulsion components. By combining advanced 3D printing capabilities with algorithmic design techniques, they are creating highly optimized and efficient propulsion systems that push the boundaries of what’s possible in spacecraft design.
How ProtoTech Solutions Contributes to the Spacecraft Design Industry

3D printing is more than just a tool, it’s a paradigm shift for spacecraft design. By enabling the creation of lightweight fuel tanks, complex engine parts, and other innovative components, it’s helping us build the next generation of spacecraft that are faster, cheaper, and more capable. As we set our sights on Mars, the Moon, and beyond, this technology will play a starring role in making those dreams a reality.
Focuses on areas like Solid Modeler programming (using technologies like ACIS, Granite, and Parasolid), 3D graphics (DirectX, HOOPS, OpenGL), and user interface development (MFC, Qt). These skills are highly relevant to the design, simulation, and optimization processes that are critical for 3D printing applications, including spacecraft design. Here’s how ProtoTech Solutions likely helps in this space:
- Software Tool for 3D Printing Design: ProtoTech’s expertise in CAD/CAM/CAE software development makes it a valuable partner for companies and organizations working on 3D printing for spacecraft. We can develop custom software tools that help engineers design complex spacecraft components, such as lightweight fuel tanks and intricate engine parts.
- Visualization: Our proficiency in 3D graphics (DirectX, HOOPS, OpenGL) is another area where we can contribute. Visualizing how 3D-printed spacecraft parts will look and function is critical for design validation and stakeholder communication. We develop tools that could help create detailed 3D models and animations of spacecraft components, such as those used in NASA’s visualizations of 3D-printed thermal protection systems or pressure vessels.
By combining these capabilities, ProtoTech Solutions plays a crucial role in advancing spacecraft design processes, enabling more efficient, accurate, and innovative approaches to creating the next generation of space exploration vehicles.